Back to DIY Advice
DIY Laminate Flooring Installation Pitfalls to Avoid
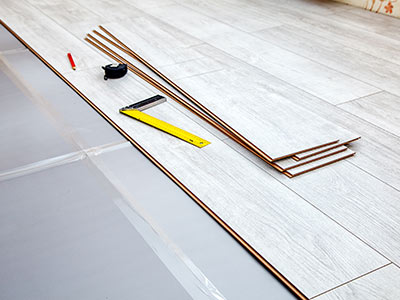
Laminate flooring can instantly transform the look of any room with its realistic wood or tile finishes. But installing laminate flooring yourself can lead to costly mistakes that damage your floors or cause them to fail prematurely if you're not careful. This article will cover the 10 most common laminate flooring installation mistakes homeowners make along with tips to avoid them. Follow these laminate installation guidelines to ensure your floors look pristine for years to come.
Not Allowing Floors to Acclimate
One of the biggest laminate flooring installation mistakes is not allowing the planks to acclimate to the environment first. Acclimation is the process of allowing the floors to adjust to the temperature and humidity of the room where they will be installed. Most laminate flooring manufacturers recommend letting the sealed boxes of planks sit in the installation room for 48 hours before installation. But why is acclimation so important for laminate floors?
When the planks adjust to the proper indoor temperature and humidity levels, it prevents issues like gapping, buckling or warping after installation. Drastic changes in temperature and humidity can cause the planks to rapidly contract or expand. By not allowing the floors to acclimate before installing, you risk the planks shrinking or swelling excessively once the temperature or seasons change. Then you’ll end up with visible gaps between planks or buckled, warped boards.
Always check the manufacturer’s recommendations and allow floors to acclimate for at least 48 hours. Leaving the boxes sealed during this period prevents the planks from taking on excess moisture. Opening the boxes too soon can sabotage the acclimation process. Proper acclimation leads to stable floors that won't shift, gap, or buckle down the road. Don't skip this crucial first step when installing laminate flooring.
Using the Wrong Tools
Installing laminate floors is an easy DIY project, but only if you use the proper tools. It's important to avoid hammering the planks into place. The impact can damage the locking systems that connect the planks. Instead, use a tapping block to gently tap the planks together without harming the connections. A rubber mallet can also work in a pinch.
You'll also need a pull bar for manoeuvring the planks into place and tightening up the joints. Pull bars protect the edges from chips and dents that hands and hammers can cause. Choosing quality underlayment is also critical for smooth, quiet, and durable floors. Cork, felt, or foam underlayment helps smooth out subfloor imperfections. They also provide moisture protection, insulation, and sound absorption.
But paper or plastic sheeting are not suitable underlayments. These thin materials won't effectively pad the floors or prevent noise. Lastly, spacers are a must-have tool for maintaining the proper expansion gap around the perimeter. Spacers ensure you leave an even 1/4 or 1/2 inch gap required for the floors to expand and contract. Having the right laminate flooring tools on hand will make the installation process safer for the planks and easier on your knees. Don't risk damaging the flooring by using improper tools or skimping on the underlayment.
Forgetting the Underlayment
In the rush to get started on installation, some DIYers accidentally skip the underlayment. But underlayment is never optional with laminate floors. Quality underlay acts as a moisture barrier, insulates against sound, and smooths out minor subfloor imperfections. Without underlayment, you'll likely end up with hollow or noisy-sounding floors. Laminate planks installed directly over a plywood or concrete subfloor transmit noise throughout the room. Underlayment helps muffle footsteps, furniture shuffling, and other sounds.
Underlayment also protects against moisture damage by creating a barrier between the planks and the subfloor. Moisture seeping through a concrete slab can warp planks over time without an underlayment moisture barrier. Underlay evens out small bumps or dips on the subfloor. Underlayment foam or felt layers help prevent uneven spots from telegraphing through to the surface.
Don't forget this crucial step when assembling your tools and materials. Quality underlay is essential for quiet, well-insulated floors free of uneven spots. Take the time to install underlayment first before starting your laminate flooring installation.
Not Checking for Level Subfloors
Uneven, unlevel subfloors are a common problem that can ruin a laminate flooring installation. Small dips and bumps on the subfloor will transfer to the surface, creating an uneven floor. Gaps can also appear between planks installed over uneven spots. That’s why it’s critical to check that the subfloor is flat and level before starting installation. Use a long straight edge and level to find any low or high points on concrete or plywood subfloors.
For each high spot, sand or grind down the concrete. Fill any low spots with floor leveler compound once the high points are addressed. Unlevel subfloors can also cause planks to pop apart after installation. When gaps appear, debris works its way underneath and causes the locking systems to disengage.
A flush, even subfloor prevents costly issues down the road like unlocking planks, premature wear, and damage to locking systems. Take the time to assess the subfloor and correct any imperfections first. While laminate is more forgiving than natural wood, significant dips and bumps will still transfer through. Starting with a flat, smooth subfloor ensures your floors look great for years and resist damage from uneven wear or unlocking planks.
Not Following Expansion Gap Rules
One of the most frequent complaints after a DIY laminate flooring installation is boards that have buckled or warped. Often, the culprit is forgetting to leave the proper expansion gaps during installation. Laminate floors require a small gap between the boards and the walls, as well as any other fixed vertical obstacles like stairs or cabinets. This expansion gap gives the floors adequate room to expand and contract with normal fluctuations in humidity and temperature.
For laminate flooring, the expansion gap should be at least 1/4 inch around the perimeter. Some manufacturers recommend a slightly larger 3/8 to 1/2 inch gap. Use spacers against the wall studs when installing your first row to maintain an even gap as you work across the floor. If the gap around the edges is too small, the floors will push up against the wall as they expand. This can lead to buckled or warped boards, damage to the locking systems, and boards trying to separate. Leaving proper expansion gaps prevents costly damage.
Don’t forget to also leave expansion gaps where the flooring meets door jambs, stairs, kitchen islands, pipes, and any other fixed objects. Take the time to calculate the proper gap size recommended and use spacers to maintain it throughout the installation.
Improper Alignment When Placing Planks
Achieving the right pattern alignment is one of the trickiest parts of a DIY laminate flooring installation. Proper alignment creates an even, seamless appearance across the floor. One common mistake is failing to stagger the end joints between rows. Staggering the seams means the end joints between planks should be offset by at least 6 inches from row to row.
If the end joints line up across multiple consecutive rows, it creates noticeable weak points in the floor. Staggering helps strengthen the overall floor by distributing weight across more planks. Uneven plank alignment within each row also leads to a sloppy finished appearance. Carefully line up the tongue and groove edges as you install each plank. Use spacers against the wall to ensure the rows stay straight.
Irregular alignment becomes especially noticeable on patterned or tiled laminate floors. The floor will look crooked rather than forming neat lines. Take your time during installation to align both the end joints and side joints properly. Use the previous row or a straight edge as a guide. Proper alignment results in durable, attractive floors that look professionally installed.
Not Using Spacers at Walls and Vertical Obstacles
Spacers are a vital tool for maintaining the proper expansion gap around the perimeter of the room and obstacles. But many DIYers try to eyeball the right gap width instead. Without spacers, it’s almost impossible to keep the expansion gap consistent as you work across the floor. Eyeballing leads to gaps that are too narrow in some spots and too wide in others.
Narrow gaps place stress on the boards when they expand, potentially causing damage. Overly wide gaps look sloppy and allow debris to work underneath the planks. Spacers take the guesswork out of maintaining the right gap width. Place them every 8 to 12 inches around the perimeter before installing the first row. Use spacers around cabinets, door jambs, and any other fixed objects too.
Look for spacers in sizes matching the expansion gap recommendation from the flooring manufacturer. For example, 1/4 inch or 1/2 inch spacers. Keep a supply on hand and insert a spacer every few planks as you install each new row. Don’t rely on your eyes alone to achieve consistent spacing. Let spacers do the hard work for flawless results.
Forgetting About Transitions at Doorways
Laminate flooring needs to be able to expand and contract freely in each separate room. Failing to allow for this movement by installing matching planks across multiple rooms can lead to gapping or buckling. The best practice is to install a transition piece in doorways between adjoining rooms. Transition mouldings, T-moldings, or threshold strips create a break between the laminate floors. Then the floors can expand independently without impacting each other.
Without a transition, the floors may buckle or pull apart at the doorways as they expand. The floors essentially become joined as one giant expanse. Make sure to plan for transition pieces early when estimating the materials you’ll need. Measure the width of your doorways to determine the length of transition strips required.
Follow the manufacturer's instructions for installing and securing transition mouldings between rooms. These important finishing pieces allow stress-free movement of your floors.
Getting Adhesive on the Plank Surfaces
When installing laminate flooring, it's important to work carefully with any adhesives or glue. Drips, spills, and overspray can easily stain or damage the surface of the planks. If using glue-down installation in areas like the kitchen, take extra care when applying the adhesive. Prevent drips by applying a thin, even layer spread with a notched trowel.
Clean up spills immediately with a damp cloth to avoid residue drying on the plank surface. Mineral spirits or lighter fluid can also help remove the dried adhesive. When using construction adhesive to secure planks in doorways or around fixed objects, apply carefully. Masking tape can help minimise oozing onto floor surfaces.
Inspect planks for any streaks or spots before installing the next row. Adhesive can foul the laminate finish, prevent connections from locking tightly, or telegraph through the surface. Work slowly when using adhesives and clean as you go. Drips and spills become exponentially harder to remove once dried. Avoid fouling the laminate plank surfaces during installation.
Neglecting to Seal Around Wet Areas
Laminate flooring and water are not compatible. Failing to properly seal the planks around sinks, tubs, showers, and other wet areas can lead to damage from moisture intrusion. Use a flexible silicone caulk to seal along the bottom edge of cabinets, around pipes, and anywhere the flooring meets plumbing fixtures. This creates a water-tight barrier to keep moisture away from the planks.
In bathrooms, a coat of waterproof sealant around the perimeter helps fortify the expansion gap. Look for sealants designed for laminate floors. Don't assume your underlayment will provide enough moisture protection alone. Take the extra step to seal around wet areas using caulk and waterproofing compounds.
If puddles or leaks occur later, the seals prevent water from being rapidly absorbed under the flooring. This gives you vital time to clean up excessive moisture and prevent permanent damage. Properly sealing and waterproofing wet areas provides an added layer of insurance. Don't find out the hard way that your floors weren't adequately protected from leaks or puddles.